Estimated reading time: 9 minutes
Harvesting and processing agricultural products can be dangerous and processing sugar is no exception. SafeRack specializes in safety and access equipment to keep workers safe in agriculture, industrial, and commercial environments. In this article, we will not only answer questions about harvesting and processing sugar, but also outline some of the equipment used in processing, bulk loading and transporting.
Sugar, chemical name sucrose, is a sweet-tasting soluble carbohydrate that occurs naturally in fruits, vegetables, and nuts.
Sugar
Most of us consume sugar daily. From natural sugars in fruits to sugar in our coffee and tea to candy and baked goods, sugar is a staple of our diets. All green plants produce sugar through photosynthesis, the process that plants use to transform sunlight into food. In addition to sugar, plants also produce glucose and fructose. Glucose and fructose are both monosaccharides, meaning that they are individual sugar units. A sugar molecule is made up of both glucose and fructose meaning that it is a disaccharide.
While all three occur naturally in plants and are sweet, there are significant differences in how they are processed by the human body. The body immediately breaks down glucose to either store it or use it immediately for energy. Fructose is metabolised primarily in the liver and produces energy through a process called glycolysis. But unlike glucose, fructose can produce fat through lipogenesis. When sugar is consumed, the body separates the glucose and fructose molecules, which are individually metabolized.
Farmers look for sugar sources that contain the least amount of glucose and fructose. Sugar beets and sugarcane are the clear frontrunners.
Processed foods, those that have been altered during preparation, have the most fructose. We can often see this on food labels as “added sugars” which are consistently linked to health issues. So, when it comes to producing sugar, farmers look for sources that contain the most sugar and the least amount of glucose and fructose. Sugar beets and sugarcane are the clear frontrunners in this regard.
Sugar Beets vs Sugarcane

Most of the world’s sugar supply comes from sugarcane. According to the International Sugar Organization, sugarcane accounts for nearly 80% of global production. Sugarcane is a type of grass that is grown in tropical and subtropical areas. The plant produces stalks that can grow upwards of 24 feet high. Sugar beets also account for a significant percentage of annual sugar production. In fact, some 60% of sugar produced in the U.S. comes from sugar beets. The highest-producing states are Minnesota, Idaho, and North Dakota.
- Sugarcane grows above ground while sugar beets grow below ground.
- Sugar beets grow in temperate climates while sugarcane grows in tropical climates.
- Most sugar beets in the U.S. are GMO while sugarcane is mostly non-GMO.
- Sugarcane is processed with bone char to make it white, and sugar from sugar beets is naturally white.
- Sugarcane Molasses is the byproduct of sugarcane production and is used to make brown sugar. Sugar beet molasses with low sugar content is often used for animal feed.
Growing and Harvesting Sugarcane

Sugarcane is planted from stalk cuttings and takes approximately 1 year to reach maturity. The harvest season runs from mid-October through mid-March, providing 4 harvests from a single planting, Sugarcane can be harvested both manually and with equipment. Farmers typically use a single-row, combine-style harvester. The sugarcane is cut at the base of the stalk, placed into in-field wagons or hopper cars, and loaded into flatbed trailers for transport to the processing facility.
Sugarcane Processing

At the processing facility, sugarcane is crushed, and the juice is heated and filtered. It is then crystallized to create raw sugar and centrifugated to remove the remaining juice. The final step involves extracting the remaining syrup which is referred to as cane mill molasses.
SafeRack’s 18′ stair tower installation at a sugar refinery in Northern California. Using ErectaStep’s in-stock modular stairs, it replaced a steep, unsafe set of stairs.
View Installation
— More on ErectaStep
Growing and Harvesting Sugar Beets

Unlike sugarcane, sugar beets start as seeds. They are planted 1 inch apart in rows and only take 90 to 95 days to reach maturity. Sugar beets are harvested from late September through October. Harvesters use a rotor beater to cut off the heads of the beets, which are left in the field. A beet loader then pulls the beets from the soil and places them into a truck which is driven to a processing plant.
Processing Sugar Beets
Once the harvest arrives at the processing plant, they are placed on conveyor belts. The beets are transferred to a revolving drum and showered with water. Rocks and gravel are removed. The beets are washed in a beet washer which includes a magnet that removes metal fragments. The clean sugar beets are transferred to the slicers. They are cut into small pieces that resemble French fries. This process makes it easier for the sugar to be extracted.
The sliced beets are placed in a large hot water tank and soaked to allow the sucrose to be extracted by osmosis. The resulting brown sugary pulp then enters a diffusion chamber to extract as much sugar as possible. The waste is used for animal feed or as a fertilizer. The juice then enters the purification process. Impurities are removed by adding milk of lime and carbon dioxide. The residual juice is put through another filtration process which produces a “thin juice” with a relatively low sugar content. To increase the content, it is then boiled leaving a “thick juice.” The “thick juice” goes through a crystallization process, is dried, and packaged.
Sugar Processing Equipment
A facility may only do certain parts of the sugar processing, and then store some of the by-products at another facility. This was the case with a recent SafeRack customer located in Florida. The customer would process the sugar beets and send the molasses off to another storage location to eventually be sent for further processing into animal feed.
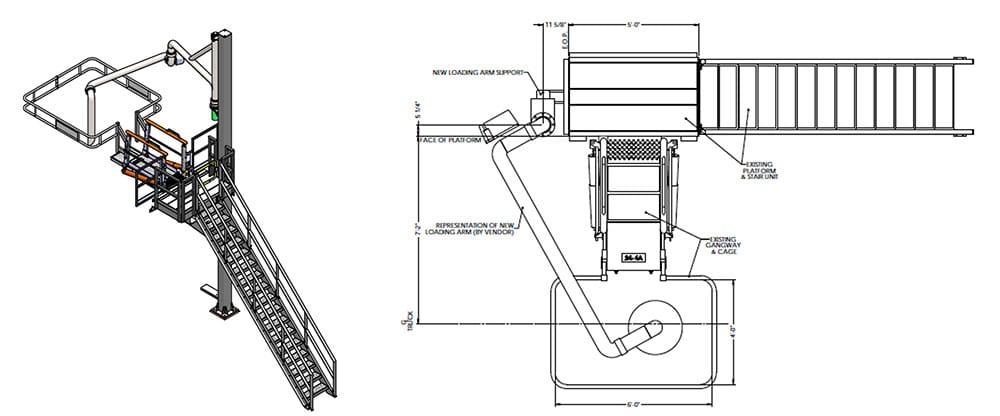
Transporting the product often requires the use of a railcar or truck tanker. This presents unique logistical and safety challenges that need to be considered. If moving liquids, there are generally pipes to carry the product from the processing locations to the storage tanks. From there, the liquid goes from the storage tanks to the truck tanker or rail cars. All of this is done without the possibility of harm to any operators. But that all changes at the point of transfer from the pipe to the transportation vehicle.
It’s at this point where the operator must access the top of the truck or railcar and connect the product hose or loading arm to the delivery vehicle. That access is not an easy or inherently safe task and requires specialized equipment to ensure that the operator can safely access the valves, connect the pipe via a hose, hose reel, or railcar loading arm, and fill the vessel. There are many types of equipment that can be used. But typically a common loading situation involves the use of stairs leading up to a platform. A gangway deploys from the platform to the top of the tanker or rail car. A safety cage adds another layer of safety for the operator. The image below depicts a common single loading rack layout. NOTE: Where a safety cage is not used, one can find Self Retracting Lifelines (SRL) that are connected to an overhead tie-off point or track.
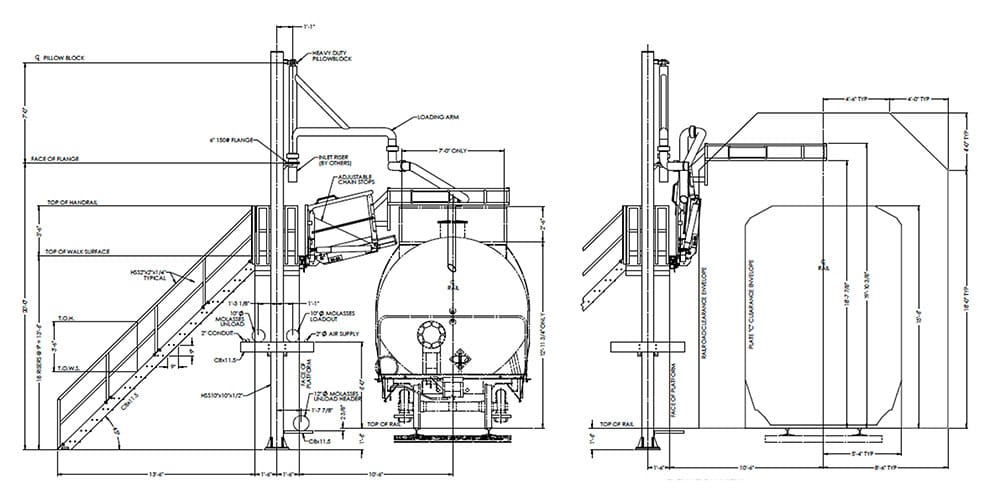
In some cases, operators may need additional protection which includes the possible use of railcar loader canopies for shade, or perhaps an air-conditioned building that sits on the platform. Some operations require a longer platform if an operator needs to access multiple rail cars and not have to go up and down multiple sets of metal stair platforms. There are all kinds of ways to make operators both safe and comfortable, you just need to make sure that you talk to an expert who can help guide you through the process and choose the best railcar loading systems for your operation.
Before & After

SafeRack is your Trusted Partner helping you execute your transformative projects into highly efficient and safe loading and unloading operations. Our unparalleled in-depth knowledge of the sugar processing industry covers:
- Waterway, road, or railcar loading and unloading
- Spill containment for pallets, trucks, rail cars & berms
- Grounding & overfill protection for truck & railcar
- Fall protection trolley beam & lifeline fall arrest systems
- Many other accessories
